

This practical project can be put to good use in almost any laundry room, mud room or kitchen. Use it to dry clothes, towels, even flowers or herbs. Ours is made from ash, but oak, maple, birch arid pine are other good choices.
Step 1 : Prepare the Stock
- 3/4 in. thick stock for the upper rail (A)
- Shelf (B)
- Lower rail (C)
- Two stiles (D)
- Two sides (E)
- Dozen long stretchers (F)
- Four short stretchers-made from l/i in thick stock (G)
- 1/2 in. diameter birch dowel stock for the long dowel (H)
- 11 short dowels (I)
**We used clear stock, although boards with a few small, tight knots are perfectly suitable. A board that measures at least 5 in. wide and 40 in. long will provide enough material for all the stretcher parts. It"s best to use clear stock here, as the stretchers are relatively small. A knot in the wrong location might weaken a stretcher enough to cause it to break under the weight of several wet bath towels. Be a little choosy when selecting the dowels at your hardware store. You"ll want them to be reasonably straight and free from small knots that sometimes show up. Also, try to avoid those that are badly out of round.
Step 2: Cut all parts to the dimensions shown in the Bill of Materials (Except the long and short dowels)
- Check your table saw, along with the rip fence and miter gauge, as you"ll want all the cuts to be square.
Step 3: Make the Upper Rail and Shelf
- Transfer the profiles of these parts from the grid pattern to the stock
- Cut them out with the band saw
- Sand the sawn edges smooth (Disc sander is suggested)
**We added a slight chamfer (about 3/16 in.) along the long curve of each part. As shown in the exploded view, the chamfer ends at the ""notch"" in the curve. You can do this with a hand plane or, as we did, with a router table equipped with a 45 degree chamfering bit. Since the upper rail mounts against the wall, there is no need to chamfer the curve on the back of this part.
Step 4: Make the Sides
- Lay out and mark the location of the two, 3/4 in. wide by 2 in. long, notches on the back edge of each side.
- Using the table saw make the 3/4 in. deep cut first
**The stock was supported by the miter gauge as it passed, on edge, through the blade. The 2 in. long leg of the notch was cut with the band saw. If you have one, use a wide band saw blade here (3/4 in. is fine), as it will tend to cut straighter than a narrow blade.
- Use either the front edge or the upper rail and shelf as a template to trace the curve on each side
- Then cut them out on the band saw
- Sand the edges smooth
- Lay out and mark the centerline location of the 1/2in diameter by 3/8 in. deep hole thats bored in each side to accept the long down (refer to end view)
**You"ll want the hole square to the side, so use the drill press here.
Step 5: Bore the Stretcher Holes
**As shown in the end view, all the long and short stretchers have a 1/2 diameter hole bored 1/2 in. from each end. In addition, the long stretchers have a 1/2 in. diameter hole bored in the middle. All totaled, there are 44 holes to be bored, so some sort of locating setup on the drill press makes a lot of sense. The setup need only be a 3/4 in. square by 16 in. long fence clamped to the drill press table, with a spring clamp firmly securing a stop block in place (see photos).
- Make a couple of test holes in scrap stock
- Make the end holes first, locating the fence and stop block to establish the proper hole centerline.
- Relocate the stop block to accommodate drilling the middle hole on the long stretchers
**When boring the holes, it"s a good idea to always keep the same edge of the stretcher against the fence. Doing so will help insure that the holes line up pretty well, even if they are slightly off center in the drill press setup.


Drill the Pieces - Click the diagram to open in a new tab
Step 6: Assemble Stiles To Sides
- Add a thin coat of glue to the mating surfaces
- Apply clamp pressure
- Drive three or four small brads along the edge of each stile (In order to prevent the parts from sliding out of position when the clamps are tightened)
- Then snip the heads off so that about 1/16 in. is exposed
- Allow the parts to dry thoroughly before removing the clamps.
- Scrape away any glue that may have squeezed out of the joint
**When joined, the back of the stiles should be flush with the back edge of the
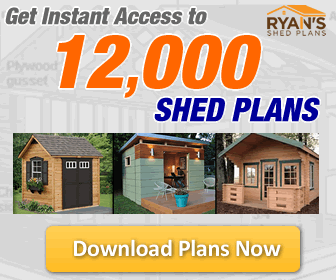

Drying Rack Bill of Materials -
Click to enlarge in a new tab
Step 7: Test Assemble
**At this point, it"s a good idea to test assemble the parts to make sure everything is fitting up okay. It will also enable you to determine the exact length of the long and short dowels.
- Use 3/4 in. long by no. 8 flathead wood screws to attach the stile/side subassembly to the upper rail and the lower rail (as shown in the exploded view, a single screw is all that"s used at each joint)
- Attach the shelf to the top end of the sides and to the upper rail using the same size screw (just one screw joins the shelf to the sides, while three screws secure it to the upper rail)
- Measure the distance between the two sides
- Cut the dowels to length (the long dowel should extend at least 1/4 in. into the 3/8 in. deep hole in each sides. The short dowels should be cut about 1/16 in. less than the distance between the sides)
Step 8: Sand and Finish the Parts
- Remove the screws from the assembled rack so that all the parts, including the stretchers and dowels, can be final sanded
- Sand each of the parts thoroughly, finishing with 220-grit (take particular care when sanding the dowels, as rough edges will easily snag on delicate fabric)
- Apply two coats of varnish to all parts except the stretchers and dowels (don"t use shellac or any other of the clear finishes that won"t stand up well to dampness or moisture)
- Recommended to not stain stretchers and dowels, as some stains tend to "bleed".
**Before final assembly, we applied two coats of varnish to all parts except the stretchers and dowels. The stretchers and dowels were left unfinished. It"s a good idea not to stain the stretchers and dowels, as some stains tend to ""bleed."" If that happened, your favorite sweater might come off the drying rack with an unwanted accent stripe.

Step 9: Assemble the Rack
**Looking at the exploded view, you"ll note that each end of the rack has three long stretchers and a short stretcher on the inside, and three long stretchers and a short stretcher on the outside.
- Insert three short dowels through the middle holes of the long inside stretchers (note that the dowels must extend through the holes the 1/2 in. thickness of the stretcher stock)
- Bore a pilot hole to help keep the stretcher and dowel from splitting
- Drive a 7/8 in. long brad through the edge of each stretcher and into the dowel once you have the dowel extending the right distance
**When joining these parts, you must make sure that the stretchers are lined-up (parallel) with each other when viewed the long dowel) can be dry assembled to the " H " sub-assemblies. We found that everything tends to stay together better if the assembly is done with the parts on end as shown.
- Close-up the rack
- Use a clamp and a couple of pieces of scrap stock to help hold the upper parts together (Photo B)
- Carefully lay the assembly on the workbench as shown in Photo C.
- Drill pilot holes for 7/8 in. long brads in each end of the outside stretchers with the rack in the closed position (do one end at a time, first drilling the pilot hole, then driving the brad)
**Do not add a brad to the middle hole of the long stretchers, or to the ends of the two inside short stretchers. A brad in any of these holes will prevent the rack from opening. Because the two inside short stretchers don"t have a brad at either end, they may slide out of position a bit if the rack is used a lot. We solved the problem by slipping a small rubber "O-ring" on each end of the dowel before assembly (see detail). You can find "O-rings" in the plumbing section of your hardware store. As another option, you can drive a short brad into the dowel just inside each stretcher.
Step 10: Final Assembly
- Attach the upper and lower rails to one of the stile/side sub-assemblies. using the screws from the test assembly done earlier
- Slide the long dowel through the stretcher holes in the rack and into the pivot hole in the side
- Then add the other stile/side
- Attach the shelf to complete the assembly.
**By the way, the screws provide plenty of strength, so there is no need to add any glue to these joints. And, by not using glue, you"ll be better able to make repairs should any part of the rack ever get damaged.
- Check to see that everything operates smoothly as it"s opened and closed with the parts assembled
- Mount the rack securely to the wall
**Ours is mounted with two screws driven through the upper rail, just under the shelf. They were spaced 16 in. apart so that we could be assured of screwing into two wall studs.
Original article and pictures take http://www.rockler.com/how-to/build-a-drying-rack/ site
>
Комментариев нет:
Отправить комментарий