



I would like to make a couple of comments about the construction process if I may.
I think the general idea is very good. However, the manner of construction is not so good.
1) Never drive screws into end grain timber. Always screw into cross grain. There is no real strength in end grain fixings.
2) Never drive screws down through the length of the upright support. Always screw through the base board into the support.
3) Make sure the motor support upright is wider than the support bracket. Cut a rebate into the support that is just wide enough to accept the motor bracket. Don"t forget the end grain rule. The rebate must be cut square to the centre guide and level to the base board. The bracket must be a close fit in the rebate. I"m English, that is how we spell centre.
4) You"ll need more than two screws to support the tail stock support bracket.
5) The head stock support will have to be re-designed to prevent any unwanted movement when machining is taking place. A wider block is probably all that is needed.
6) What isn"t obvious is how you fix the whole to your work surface.
Sounds like Jim has an axe to grind. Did someone throw his toys away?

I would like to make a couple of comments about the construction process if I may.
I think the general idea is very good. However, the manner of construction is not so good.
1) Never drive screws into end grain timber. Always screw into cross grain. There is no real strength in end grain fixings.
2) Never drive screws down through the length of the upright support. Always screw through the base board into the support.
3) Make sure the motor support upright is wider than the support bracket. Cut a rebate into the support that is just wide enough to accept the motor bracket. Don"t forget the end grain rule. The rebate must be cut square to the centre guide and level to the base board. The bracket must be a close fit in the rebate. I"m English, that is how we spell centre.
4) You"ll need more than two screws to support the tail stock support bracket.
5) The head stock support will have to be re-designed to prevent any unwanted movement when machining is taking place. A wider block is probably all that is needed.
6) What isn"t obvious is how you fix the whole to your work surface.
Sounds like Jim has an axe to grind. Did someone throw his toys away?

I would like to make a couple of comments about the construction process if I may.
I think the general idea is very good. However, the manner of construction is not so good.
1) Never drive screws into end grain timber. Always screw into cross grain. There is no real strength in end grain fixings.
2) Never drive screws down through the length of the upright support. Always screw through the base board into the support.
3) Make sure the motor support upright is wider than the support bracket. Cut a rebate into the support that is just wide enough to accept the motor bracket.
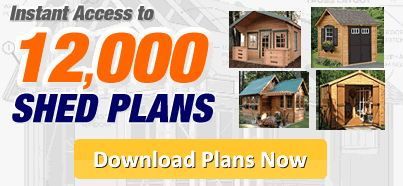
4) You"ll need more than two screws to support the tail stock support bracket.
5) The head stock support will have to be re-designed to prevent any unwanted movement when machining is taking place. A wider block is probably all that is needed.
6) What isn"t obvious is how you fix the whole to your work surface.
Sounds like Jim has an axe to grind. Did someone throw his toys away?

I would like to make a couple of comments about the construction process if I may.
I think the general idea is very good. However, the manner of construction is not so good.
1) Never drive screws into end grain timber. Always screw into cross grain. There is no real strength in end grain fixings.
2) Never drive screws down through the length of the upright support. Always screw through the base board into the support.
3) Make sure the motor support upright is wider than the support bracket. Cut a rebate into the support that is just wide enough to accept the motor bracket. Don"t forget the end grain rule. The rebate must be cut square to the centre guide and level to the base board. The bracket must be a close fit in the rebate. I"m English, that is how we spell centre.
4) You"ll need more than two screws to support the tail stock support bracket.
5) The head stock support will have to be re-designed to prevent any unwanted movement when machining is taking place. A wider block is probably all that is needed.
6) What isn"t obvious is how you fix the whole to your work surface.
Sounds like Jim has an axe to grind. Did someone throw his toys away?

I would like to make a couple of comments about the construction process if I may.
I think the general idea is very good. However, the manner of construction is not so good.
1) Never drive screws into end grain timber. Always screw into cross grain. There is no real strength in end grain fixings.
2) Never drive screws down through the length of the upright support. Always screw through the base board into the support.
3) Make sure the motor support upright is wider than the support bracket. Cut a rebate into the support that is just wide enough to accept the motor bracket. Don"t forget the end grain rule. The rebate must be cut square to the centre guide and level to the base board. The bracket must be a close fit in the rebate. I"m English, that is how we spell centre.
4) You"ll need more than two screws to support the tail stock support bracket.
5) The head stock support will have to be re-designed to prevent any unwanted movement when machining is taking place. A wider block is probably all that is needed.
6) What isn"t obvious is how you fix the whole to your work surface.
Sounds like Jim has an axe to grind. Did someone throw his toys away?


For future instructables, I would suggest that a video and a few pictures are not enough. Generally, on this site I expect to see a complete list of necessary supplies (including the source) and a complete step-by-step set of written instructions. A video is a nice add-on but cannot be the only source for info. Otherwise there"s no benefit coming here over YouTube. As Jim noted, this really just looks like an ad for your youtube video, which isn"t appropriate, in my opinion. I"d like to see you build this out with full information so I can build this - I"d love one for my workshop but even the video didn"t contain enough information on supplies and process for me to do that.
I agree. However, there actually are a lot of Instructables that have a video as the only source of info, so it is acceptable, if not preferred.
I find videos very helpful because I can see it being done, which is often easier than making sense of written instructions. That is, when I can concentrate long enough to watch a video. This one was short and to the point, the way I like it. But, since I have no clue what he was talking about, it is useless to me without the writen instructions.
It is simply not true that electric motors necessarily run at fixed speeds; that that would depend on the type of motor. Some a.c. induction motors run efficiently at lower speeds with much reduced power output if you reduce the A.C. frequency in proportion to the reduction on voltage, in a constant volts/Hz control, for example. Too low a speed can result in cogging in many motors. Many d.c. motors can be run below rated speed if not required to deliver so much torque for a long period of time without extra cooling, and some can be run a bit above rated speed if properly cooled. Some windings and bearings, however, suffer (blow out) if run at higher than rated speeds, and also could fail without extra cooling. Really efficient commutation helps with the heat problem, and there are various means to smooth chopped commutation power sources to deliver cleaner power to the motor (displacing some of the heat problem to your power conditioning electronics.)
Nope, not on a synchronous induction motor! If you are in a safe heat range for the motor, and the armature could stand the higher speed (would not throw winding, for example, and bearings were OK, then a higher drive frequency with the proportionately higher voltage would deliver more speed (and power). Nothing wrong with pulleys, a larger breadboard for this lather, a percussive drive to a jackshaft, etc to use an appliance motor and mechanical advantage changes to change speeds. If the 30 minutes lather doesn"t do the job for you, then bring yourself up to really old technology levels and use pulleys or gears, the former being much cheaper and simpler to implement. If you want many speeds, then get a set of sheaves matched for no change in belt length or else provide a single drive sheave with multiple driven sheaves and a slider on the motor to accommodate the diametral change in the driven pulleys. I"m sure you could figure that out.
I would like to make a couple of comments about the construction process if I may.
I think the general idea is very good. However, the manner of construction is not so good.
1) Never drive screws into end grain timber. Always screw into cross grain. There is no real strength in end grain fixings.
2) Never drive screws down through the length of the upright support. Always screw through the base board into the support.
3) Make sure the motor support upright is wider than the support bracket. Cut a rebate into the support that is just wide enough to accept the motor bracket. Don"t forget the end grain rule. The rebate must be cut square to the centre guide and level to the base board. The bracket must be a close fit in the rebate. I"m English, that is how we spell centre.
4) You"ll need more than two screws to support the tail stock support bracket.
5) The head stock support will have to be re-designed to prevent any unwanted movement when machining is taking place. A wider block is probably all that is needed.
6) What isn"t obvious is how you fix the whole to your work surface.
Sounds like Jim has an axe to grind. Did someone throw his toys away?
Original article and pictures take http://www.instructables.com/id/Build-Your-Own-Wood-Lathe-in-30-Minutes/ site
">
Комментариев нет:
Отправить комментарий