
Most of us think of concrete as a practical material, but it"s also one of the most versatile decorative materials around. It can take on just about any color or shape. And surface treatment options are endless. You can cast “fossil” imprints using leaves,
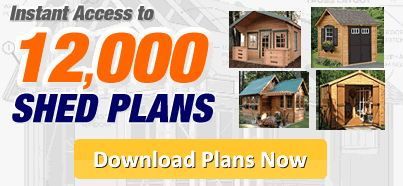
If you want a tabletop that’s elegant enough for any indoor setting and tough enough to withstand outdoor weather, you’ve found it. Tables similar to this one sell for hundreds at garden centers and outdoor furniture stores. But you can make one yourself for $50 to $100.
Your cost will depend mostly on the wood you choose for the base and the concrete mix you use. You don’t need any special skills or tools, though a table saw and an air-powered brad nailer will speed up building the form. Give yourself half a day to build the form and pour the concrete and an hour to build the table base. A few days after casting the top, you’ll spend a couple of hours removing the form, chipping the edges and applying a sealer.
Melamine-coated particleboard is the perfect form material for this project because it’s smooth, water-resistant and inexpensive. Cut the form parts as shown in Figure A. The two long sides overhang the form for easier removal later. A brad nailer is the fastest way to assemble the form (Photo 1). If you use screws or drive nails by hand, be sure to drill pilot holes to avoid splitting the particleboard. Whatever fastening method you use, space fasteners about 6 in. apart and make sure they don’t create humps inside the form.
Next, caulk the inside corners to seal the form and create rounded edges on the tabletop (Photo 2). Do this even if you plan to chip off the edges later. Use colored silicone caulk, which will show up well against the white Melamine. That way, you can easily spot and clean off smudges. Keep in mind that every tiny imperfection on the form will show up on the finished tabletop.
For neat caulk lines, run masking tape about 3/16 in. from the corners. Apply the caulk one side at a time, smooth it with your finger and remove the tape quickly before the caulk skins over (Photo 2). The tape ridges along the caulk lines will show on the finished top and make a perfect chisel guide for chipping the edges later (Photo 8).
If you want to cast leaf or fern “fossils” in the top, first press them for a day or two in a book or between scraps of cardboard. Then lay them out on newspaper and coat them with spray adhesive. Press them onto the form so they lie perfectly flat (Photo 3). Thick stems may not lie flat and can leave imprints that are too deep. To avoid this, we shaved some of our fern stems down with a razor blade.
It’s easy to embed small decorative objects in the concrete top. Unlike the casts of ferns and leaves, which leave only the imprint behind, an inlay stays in place permanently. You can inlay anything that’s durable and has crisp edges. Tiles and colored glass are the most common inlays, but you can also use coins or other metal objects. Simply spread a thin coat of silicone caulk over the face you want exposed and press it down on the Melamine base. After the concrete mix hardens, carefully scrape away the silicone film left on the inlay with a razor blade. Glue inlays face down to the form with silicone caulk. Be sure to remove excess caulk that squeezes out around the inlay.
We mixed our concrete in a bucket, using a drill and a large paint mixer attachment. This method is fast, but it requires a powerful 1/2-in. drill and won’t work well with thicker mixes. Instead, you can use a garden hoe and a plastic cement tub. Be patient and mix thoroughly so you completely wet all the powdered ingredients. Pay attention to the product’s mixing instructions, especially the recommended amount of water. An extra cup of water can make the mix too thin.
Set your form on a solid surface and level it both front to back and side to side. Otherwise one side of your top will be thicker than the other. Then pour in the mix around the edges to get an even distribution of material (Photo 4). Pouring the entire mix in the middle might concentrate the heavier particles there and weaken the edges. Wear plastic gloves as you work the material into all corners and edges (Photo 5). Use a gentle touch, however, if you have fragile objects glued to the bottom. If the mix you use requires wire reinforcement, pour and work in about two-thirds of the mix. Then add the wire and the remaining mix.
All pours contain trapped air, which will leave holes in the finished top unless you work them out. To drive out bubbles, tap the sides and bottom of the form with a hammer and continue rapping until you don’t see any more bubbles coming up. However, if you have pea gravel or other “aggregate” in your mix, limit your tapping. Otherwise, the aggregate will settle to the bottom and weaken or perhaps ruin the appearance of your table. And keep in mind that the tabletop doesn’t have to be perfectly smooth. A few holes or imperfections in the surface may simply add more natural character.
When you’re finished, cover the top with plastic and let the concrete harden and cure anywhere from four hours to two days, depending on the brand.
To remove the form, pry off the long sides and then the short sides. Pry against the form base rather than the concrete. If you have to pry off the form base, use a plastic putty knife; metal will mar the surface (Photo 6). If your top has imprints with fine detail, cover it with plastic and let it harden for an extra day. Then scrub with water (Photo 7). Use a plastic putty knife to scrape off Melamine residue that won’t scrub off.
The mix we used chips off neatly for a rough edge look (Photo 8). Be sure to set the top on plywood on a solid surface. We used a 3/4-in.-wide cold chisel, but you can use whatever width best produces the effect you want. For safety, hone down any sharp edges with a file or sandpaper.
Your top will withstand outdoor weather, but it’s susceptible to stains. To prevent them, and to bring out more color, we recommend that you seal it with an acrylic sealer (sold in the tile aisle at home centers). The first coat will sink in and the surface will remain dull. After it dries, apply a second coat, and perhaps a third, until the surface retains a shine.
Well done! Chances are that once you complete one top, you’ll want to make another.
The best concrete mix for this project is a countertop mix, which pros use to cast concrete countertops. Ask for one at a local concrete products dealer (do an online search for “concrete countertop mix”). You’ll need about 50 lbs. of mix to make the 17-in. x 34-in. x 1-1/2-in. top shown. The different brands available share one key factor—special additives called “super-plasticizers,” which allow you to add less water. Less water means a denser, stronger top. Some mixes contain fibers to help prevent cracking. Others require wire reinforcement.
You can buy color additives when you buy the mix, or buy concrete color from a more limited selection at a home center. We added 5 ozs. of charcoal liquid cement color to our 50-lb. sack of mix to get a gray, slate-like color.
Original article and pictures take http://www.familyhandyman.com/masonry/build-your-own-concrete-table/step-by-step site
">
Комментариев нет:
Отправить комментарий