

You could build this system with just a few hand tools, a drill and a circular saw, but a table saw would save you lots of time. The skills you"ll need are as basic as the tools. If you can make long straight cuts and screw parts together, you can build this system.
This whole system is made from just two materials: plastic-coated particleboard, usually called "melamine," and construction-grade pine 1x4s. (Melamine is the type of plastic used as the coating.) You could use 3/4-in. plywood or particleboard, but I chose melamine because it didn"t require a finish.
The materials for this floor-to-ceiling system cost about $37 per linear foot of wall space. That"s less than I would have paid for wimpy "utility" cabinets at a home center. Our garage walls were 10 ft. tall. If your ceiling is about 8 ft. tall, you can eliminate the deep upper cabinets. That will lower the cost to about $27 per linear foot. If you opt for completely open shelving and skip the cabinet doors, your cost will drop to about $20 per linear foot.
Roughly block out the cabinet locations on the wall, using masking tape. Remember to space the garage cabinets to leave room for shelves in between. Experiment with different cabinet widths and spacing until you find a layout that works well. Follow these guidelines:
- Each cabinet must have at least one stud behind it so you can fasten the cabinet securely to the wall.
- Limit door widths to 24 in. or less. To cover a wider opening, install double doors. We limited most of our doors to 12-in. widths so that we could open them even when the car was parked in the garage.
- Shelves longer than 2 ft. often sag. If you make yours longer, stiffen the melamine by screwing 1x4 cleats to the undersides.
- Size your cabinets to make the most of a full sheet of melamine. By making our cabinets 16 in. deep, for example, we were able to cut three cabinet sides from each sheet with no wasted material (see Figure A for other dimensions). Don"t forget that your saw blade eats up about 1/8 in. of material with each cut. Some sheets of melamine are oversized by about 1 in. to account for this.

Most home centers carry melamine in 4 x 8-ft. sheets (about $25), usually only in white. For colors other than white, try a lumberyard that serves cabinetmakers. These suppliers often charge more (about $40 per sheet) and might sell only to professionals, so call before you visit.
Home centers carry plastic iron-on edge banding. Some also carry peel-and-stick edge banding, which lets you skip the ironing. Either way, white will be your only choice at most home centers. If you want another color, go to fastcap.com and search for "Fastedge."
With your cabinet dimensions in hand, begin cutting the melamine into parts. Cut the material into equal widths for the sides and the fixed and adjustable shelves, but don"t cut the parts to length until they"re edge banded.
Here are some pointers:
Get help. Melamine is too heavy to handle solo. If you have a large, stable table saw, you and a helper can cut full sheets. But it"s usually better to slice a sheet into manageable sections with a circular saw first. Then make finish cuts on the table saw.
Wear gloves when handling large pieces. The edges of melamine are sharp
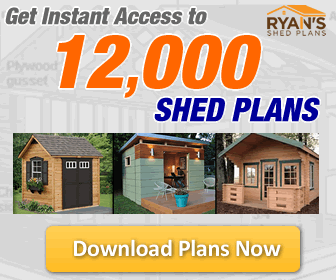
Avoid scratching the melamine surface. If your workbench has a rough surface, cover it with cardboard or old carpet. Pad sawhorses the same way. Run a few strips of masking tape across the shoe of your circular saw so it doesn"t mar the melamine.
Be careful with edges. They"re easy to chip. When you stand parts on edge, set them down gently. Don"t drop sheets or drag them across the floor.
Plan for chip-out. Saw blades often leave slightly chipped edges in the melamine coating. A new carbide blade will chip less than a dull one, but you can"t completely prevent chips. Chipping is worse on the side where the saw teeth exit the material. When you run melamine across a table saw, the underside of the sheet is particularly prone to chipping.
When you"re using a circular saw or a jigsaw, chipping is worse on the faceup side. Plan your cuts so that all the chipped edges are on the same side of the part. Then you can hide them during assembly by facing them toward the inside of cabinets.

Set your iron to the "cotton" setting and iron the banding on in two or three passes (Photo 1). On the first pass, run the iron quickly over the banding just to tack it into place. Center the banding so it overhangs on both sides. Make a second, slower pass to fully melt the glue and firmly adhere the banding. Then check the edges for loose spots and make another pass if needed. Trim the ends of the banding with a utility knife (Photo 2) before you trim the edges (Photo 3). If you damage the banding while trimming, just reheat it, pull it off and start over. Learn more about edge banding.

The adjustable shelves rest on shelf supports that fit into holes drilled into the cabinet sides (Photo 4). Drill all the way through the sides that will support shelves inside and outside the cabinet. Drill holes 3/8 in. deep in cabinet sides that form the outer ends of your shelf system. Tape wrapped around a drill bit makes a good depth marker when you"re drilling just a few holes, but a stop collar ($4) is better for this job.
Check your shelf supports before drilling. Some require 1/4-in. holes; others require 5mm holes. Use a brad-point drill bit for a clean, chip-free hole. To limit blowout where the bit exits the melamine, set a "backer" underneath. You can make a drilling guide from just about any material, but a strip of pegboard is a perfect ready-made guide (a 4 x 8-ft. sheet costs $15). Label the bottom of your guide and the bottoms of the cabinet sides so all the holes will align.

The fixed shelves that fit between the cabinet sides (A) are made from melamine panels (B) and pine 1x4s (C). Paint the 1x4s to match the melamine. Cabinets less than 4 ft. tall need only top and bottom fixed shelves. Taller cabinets also need a middle fixed shelf (Figure A). To make the fixed shelves, just cut melamine and 1x4s to identical lengths and screw them together.
Assembling the cabinets is a simple matter of fastening the sides to the fixed shelves (Photo 6). Predrill and drive a screw near the front of each fixed shelf first, making sure the banded edges of the fixed shelf and side are flush. Then drill and drive another screw near the back of the cabinet to hold the fixed shelf in position before you add the other screws. Handle the completed cabinet boxes with care—they"re not very strong until they"re fastened to the wall.
This guide takes a few minutes to make but saves time when you"re cutting the fixed shelves (Photo 5) and even more time later when you"re cutting shelves (Photo 14). Our system required 30 shelves. To make a crosscut guide, screw a guide strip to the base and run your saw against the guide strip to trim the excess off the base. Add a squaring strip positioned perpendicular to the guide strip. Position the stop block to set the length of your parts.


Make the doors after the cabinet boxes are assembled. To hang the doors, first screw hinges to the cabinets (Photo 7). The type of hinge I chose is called a "wrap" hinge because it wraps around the corner at the front edge of the cabinet. If you don"t find them at a home center, search online for "1/4 overlay wrap hinge." This design has two big advantages: It mounts more securely to the cabinet and it lets you position the doors perfectly (Photo 8) before you fasten them (Photo 9).
I used four hinges for each of our 12-in.-wide double doors. If you opt for a single wide door, use at least five hinges. The hinges themselves are strong enough to hold much more weight, but they"re fastened with just two screws each. The particleboard core of melamine doesn"t hold screws very well. So when in doubt, add more hinges.
With the hinges in place, measure between them to determine the door width (with double doors, allow a 1/8-in. gap between them). To determine the length, measure the cabinet opening and add 3/4 in. Cut the doors and set them in place to check the fit before banding the edges. When the doors are complete and screwed to the hinges, label each door and cabinet. Then unscrew the doors to make cabinet installation easier.

Don"t install the cabinets directly on the garage floor. Water puddles from dripping cars will quickly destroy particleboard. I mounted my cabinets about 6 in. off the floor—just enough space to allow for easy floor sweeping. This height also let us level the ledger and fasten it to the wall framing (Photo 10) rather than to the concrete foundation. We drove screws into the studs and sill plate.
You"ll need a helper to install the cabinets (Photo 11). Install the two end cabinets first, then position the others between them, leaving equal spaces for the shelves that fit between the cabinets. Watch out for obstructions that prevent cabinet doors from opening. End cabinets that fit into corners, for example, should stand about 1/2 in. from the adjacent wall.

The upper cabinets provide deep, enclosed storage space and tie the upright cabinets together so they can"t twist away from the wall. Instead of installing upper cabinets, you could simply run a long shelf across the tops of the upright cabinets.
The upper cabinets are simply horizontal versions of the upright cabinets; you use the same techniques and materials (see Figure C). Here are some building tips:
- Minimize measuring and math errors: Build the upper cabinets after the upright cabinets are in place.
- To allow easy installation, leave a 1/2- in. gap between the ceiling and the upper cabinets. You could leave the resulting gap open, but I chose to cover it. Here"s how: I ripped 1x4s into 1-in.- wide strips, painted the strips to match the edge band and screwed the strips to the tops of the cabinets. After the uppers were installed, I cut trim strips from 1x4, painted them and used them to cover the gap.
- You can build upper cabinet sections up to 8 ft. long. For strength and ease of installation, size the sections so they meet over the upright cabinets, not over open shelves.
- Remember to add hinge spacers (K) to dividers (J) so you can install hinges back to back.


Cut the shelves at the very end of the project (Photo 14). That way, you can take exact measurements inside and between shelves and use up any scraps. The number of shelves is up to you; I made four for inside each cabinet and six for each between-cabinet space. Install cabinet knobs or pulls after the doors are in place to make drilling a hole in the wrong location just about impossible.
Screws are the only fastening method used in this entire project. They make fast, strong joints. But screwing into melamine presents a few complications:
STRIP-OUT: As with any other particleboard product, melamine strips easily if you overdrive screws. Go easy on the drill trigger as you drive screws home. Use coarse-thread screws only. Fine-thread screws will strip every time. Longer screws also minimize stripping. If this project had been built from plywood, 1-5/8-in. screws would have worked fine. But we used 2-in. screws to assemble the boxes.
SPLITS: Particleboard splits easily. Never drive a screw into particleboard without drilling a pilot hole. We drilled 7/64-in. holes and used No. 8 screws. Even with a pilot hole, screws will split particleboard if you place them close to ends. Keep them at least an inch from the ends of parts.
COUNTERSINKING: Tapered screw heads will sometimes sink into melamine, but often they"ll strip out before the head is flush with the melamine surface. Next to an edge, they"ll crush out the particleboard. Always drill countersink holes to create a recess for screw heads. You can drill countersink and pilot holes in one stroke with a countersink bit ($4).
APPEARANCE: Even with a clean countersink hole, screw heads are a blemish in melamine"s perfect surface. For a neater look, use finish washers (photo above right) with screws that will be visible. Finish washers would eliminate the need for countersink holes.
Original article and pictures take http://www.familyhandyman.com/garage/storage/build-the-ultimate-garage-cabinets-yourself/view-all site
">
Комментариев нет:
Отправить комментарий