

Tip 1: Set cabinets on a platform

Most lower cabinets include a base or toe-kick that raises them off the floor. But Ken doesn"t build them that way. Instead, he builds a plywood platform that acts as the base for an entire row of cabinets. The platform can be under- sized to allow for a toe space or full size for a more traditional look (as shown here).
This approach has a couple of major advantages. First, cabinet construction is simpler. The cabinets are just boxes; no extended sides to form a base, no toe-kick cutouts. Second, installation is faster. Leveling one platform is a lot easier than positioning each cabinet individually. Ken sets the box 1/4 in. from walls to allow for wavy or out-of-plumb walls.

When the side of a cabinet box will be exposed, you have to hide the cabinet back"s edge somehow. The usual method is to rabbet the side and recess the back. But Ken gets a richer look with less hassle. He simply glues and nails the back to the cabinet box and hides the exposed plywood with a frame and panel for a classic look. And since the cover panel is a separate part, it"s easy to scribe it to the wall before fastening it to the cabinet.

Lots of designs have upper shelf units that rest on lower cabinets. Here"s Ken"s trick for fastening the shelf units to the cabinet top so that the screws are hidden: He sets the cabinet top on the lower cabinets and scribes it and sands it to fit the wall. But he doesn"t screw it in place yet. Instead, he positions the shelf units on the top and carefully slides the top forward just far enough so that he can drive screws into the shelf sides and dividers. After sliding the top back into place, he screws the top to the cabinets from below and screws the shelf units to the wall.

Before scribing stiles that will meet walls, bevel the back edge on your table saw. That way, you"ll have less wood to belt-sand off when you shape the edge to the contour of the wall. Ken cuts a 45-degree bevel about 1/2 in. deep, so he has only 1/4 in. of wood remaining.

Pocket screws are a standard joinery method, but Ken has a nonstandard approach. He assembles face frames with pocket screws, but without glue. He sands the frames, labels the back of each part and then disassembles them for easier finishing. Transport is easier too: Ken can pack a mile of face frame parts into his van and carry them into the house without banging up walls. The cabinet boxes need less TLC too, since they"re frameless during transport. Once on-site, Ken reassembles the frames with pocket screws and glue. For pocket joinery, Ken uses a Kreg Jig.
Most cabinetmakers use 1/4-in. plywood for cabinet backs. But Ken prefers 1/2-in. material. The thicker plywood usually adds only a few bucks to the cost of each box and eliminates the need for a hanging strip or “nailer” at the back of the cabinet. That means quicker construction and a cleaner interior look. Best of all, it allows you to drive a screw through the back anywhere, not just at the nailer.

With its tough, flawless clearcoat, prefinished ply- wood eliminates finishing hassles. But Ken uses it only for “no-show” parts like cabinet boxes and shelves. Finishing other parts to match the color and sheen of the factory-finished plywood is just too difficult. Finding prefinished ply- wood can be difficult. Your best bet is a lumberyard that caters to cabinetmakers.
Original article and pictures take
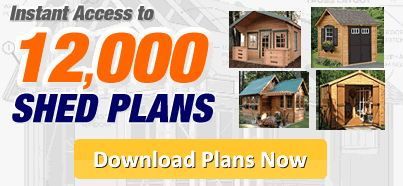
>
Комментариев нет:
Отправить комментарий